Media Platform &
Creative Studio
Magazine - Features
Circular ceramics - In conversation with artist Sara Howard
Emma Thomson
At the exhibition, there was a collection of Sara’s ceramics on display, called ‘Circular Ceramics Collection: Cup, Bowl, and Plate’.
2 June 2022

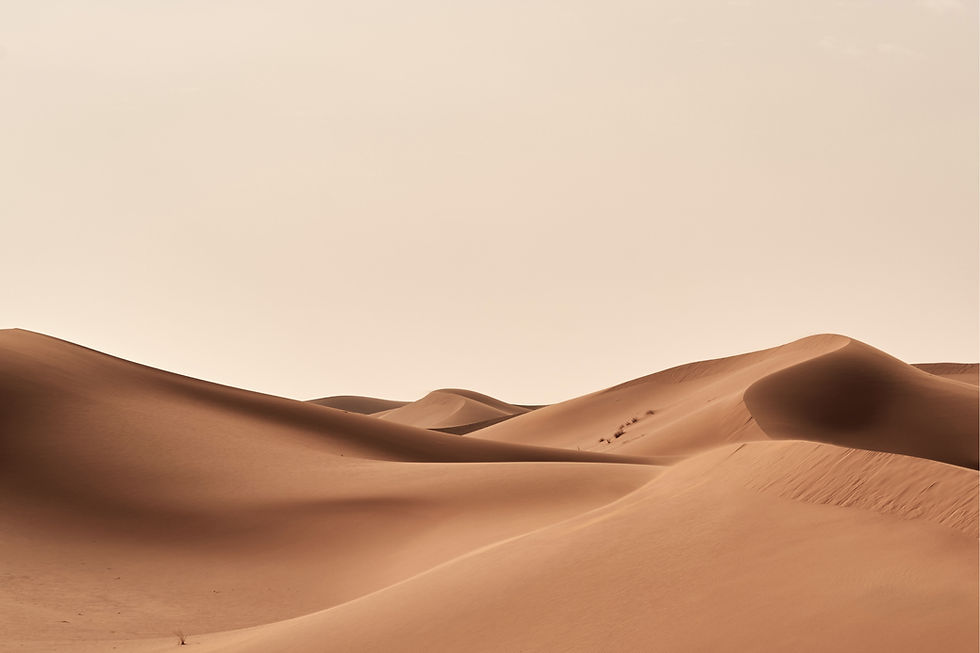

The third artist from the exhibition that I am writing an article about is Sara Howard.
At the exhibition, there was a collection of Sara’s ceramics on display, called ‘Circular Ceramics Collection: Cup, Bowl, and Plate’. I found the fact that they were made from industrial waste byproducts really fascinating. Driving past piles of waste from construction and demolition work, I had always wondered what became of it and how it could possibly be reused. It made me think about the other types of waste, such as single-use plastics, that cannot be recycled and how they could possibly be reused. The design was very minimalistic and simple, which was another appealing characteristic of the work.
I have conducted an interview with Sara to find out more about her practice and work. The interview has been edited slightly for clarity.

What materials do you use in your work and how do you reuse them?
I work with industrial byproducts that would otherwise go to landfills and with the glass stone quarry metal and construction industry to reclaim those byproducts.
In the glass industry, when they polish the edges of glass panels, this produces a hazardous glass slurry.
From the stone industry, I reclaim a stone slurry which is produced from cutting and polishing granite, quartz, and marble panels.
In the quarry industry, I work with contaminated China clay called Kaolin that does not have a high enough grade to be used in production.
Also in the metal industry, I work with companies that use laser cutters, which produce this fine powder that can be used as oxides in ceramics.
For the construction industry two months ago I set up an initiative called Golden Earth studio. It runs alongside a company called Golden Earth Developments, which is a property developer. So together we work with the construction industry to process the excavated waste which is produced when they put the foundation in for a new building. If there's clay then we'll process it and we will distribute it to makers, ceramicists, artists, schools, or educators for free.
How did you come up with the idea to reuse the materials?
I've been interested in sustainability since doing my GCSEs in high school, and I've always incorporated it into my practice. When I started my final year at BA Ceramic Design at Central Saint Martins, I set myself the challenge of producing sustainable ceramics. I didn't know how I was going to do it, I just knew that I didn't want it to be terrazzo because it seemed like the easy way out at the time.
I first looked at how I could apply the principles of the circular economy to ceramic production but learned that it was not possible. I couldn't find a way to break down clay and turn it into all its raw materials and start again. I came across industrial symbiosis, where industries exchange their byproducts to replace raw materials in another industry and I began to map out the waste streams of external industries. I looked at lots of different industries and started testing the byproducts like the materials that go into landfills. It took very intense testing, and a lot of variations in the way I was processing materials, and the way that I was incorporating them into my work. Eventually, I was able to produce ceramics made from 100% waste.

Can you talk me through the design and production process? How long does it take?
The design of the circular ceramics tableware is focused on durability, and how to prevent the end of life for a ceramic object. The tray plates are designed so that the process of producing them eliminates excess materials such as plaster, which has a limited lifespan and production. It also doesn't require any energy and it can be also scaled up for mass production.
The production process, in terms of processing the materials for production, is probably the most lengthy part. However, as I don't pay for any of the materials that I use, it balances out. That part can take about a week, but it depends. There's a lot of drying involved, crushing, grinding, and sieving, which are the boring jobs, but I do that in between everything else so I don't spend a whole day doing something like sieving for example. However, it could easily take a whole day to do that.
You've also got to factor in the collection of the materials. In London, I was cycling to all these manufacturers and I would do multiple trips on my bike because I could probably only manage 30 kilos on it at once. I would make a lot of trips, but they were all to local manufacturers so I was never cycling more than five or six kilometres, therefore, it was pretty quick.
Are there any aspects of your work that you find challenging?
Right now I am scaling up my work in Bali and that's probably the most challenging thing that I've come across so far. That's because not only am I sourcing the materials once again, but in Bali, they don't have some of the manufacturers or some of the industrial machines that you would find in London. Therefore, I can't necessarily source the same waste material that I did in London, which is challenging.
We've also got a language barrier and we've got issues with how reliable the waste streams are here. However, it's nothing that isn't manageable. For me, it's the most exciting part and it's nice to be back at square one in a way. When I guide other ceramicists in producing ceramics from waste, I'm now in their shoes as the materials aren't necessarily available everywhere.
Another aspect of my work I find challenging is being open source and sharing my work under the Creative Commons licence ‘Share Like’. The licence means that the methods are available for anyone to use, they just need to credit and release their work under the same licence. So the goal is to create a community that is able to produce sustainably because I strongly believe that sustainable solutions should not be locked away in patents. However, this does throw up problems with plagiarism, but it's something that I tackle with each issue and I just carry on doing my work. It doesn't deter me away from being open source.
I really encourage people to produce that way if they really want to have an impact. Sometimes people see open source as being naive about business but I've been able to find a way to make it work for me. I'm aware that it might not work for everyone, but I think it's really important if we have to adopt more sustainable practices sooner and reach some of the targets that the government has set before it's too late.
How do you hope to inspire people?
I think I hope to encourage people to look at being open source and the positives that can bring to your practice and also the impact that you can have by being open source. Many positives can come from working with people from a range of industries, a range of backgrounds. Without connecting with other people, I would not be able to do the work that I do. I also hope that people take the principles that I've applied in my own practice and that I've learned from other people, and they're able to apply them to their own industry or their own work, whether it's ceramics related or not. I have learnt from many different people, not necessarily from ceramists, which has allowed me to create the work that I do. I hope to pass on some of that information, and those methods of working to others who also hope to make a change.
To find out more about Sara’s work you can visit her website here, or you can find her on Instagram.
